How to Improve Supply Chain Forecasting With Predictive Analytics
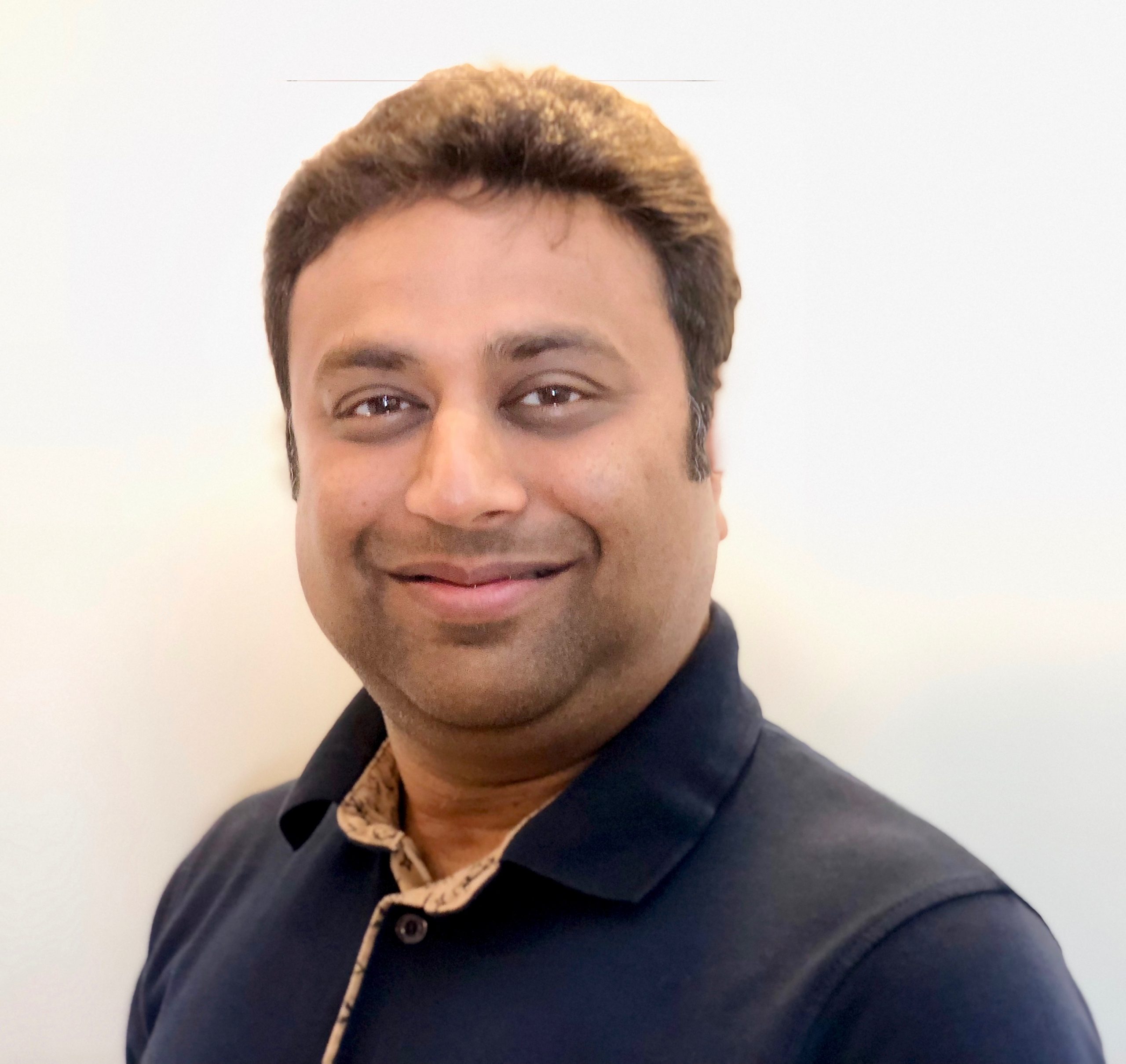
Senior Director of Global Solutions, Neo4j
5 min read
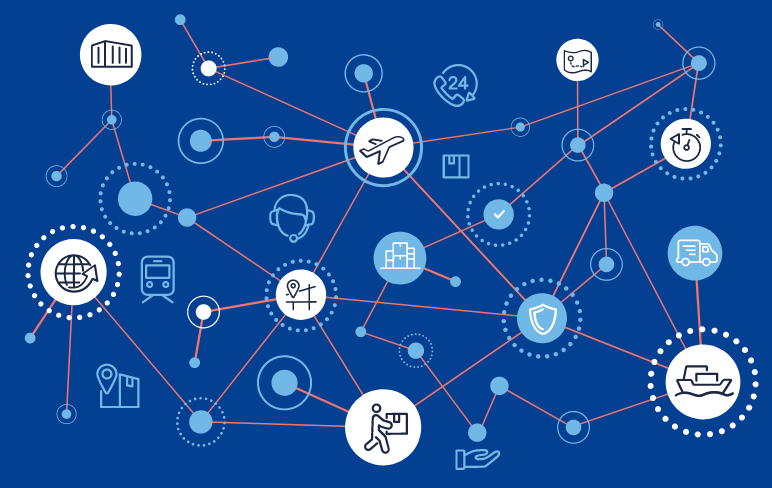
When it comes to building agile, resilient supply chains, everyone expects fast turnarounds and quick delivery, regardless of what’s happening in the world. If you don’t meet those expectations, your company’s bottom line and reputation suffer.
The good news? You can overcome potential bottlenecks in supply chain forecasting by using graph technology and predictive analytics. By applying these technical capabilities in a strategic manner, you can uncover hidden relationships in your data to make predictions about the most efficient path forward – even as circumstances shift.
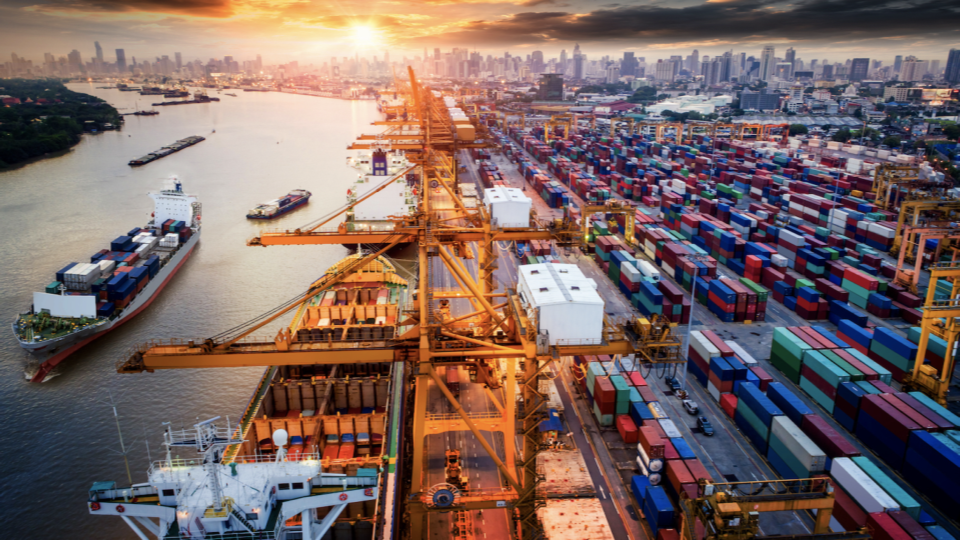
The High Cost of Supply Chain Bottlenecks and How to Avoid Them
According to a 2022 Deloitte survey, 80% of manufacturing executives reported significant supply chain disruptions in the previous 12–18 months. This is just a sample of the types of bottlenecks that grind your supply chain to a halt:
- Part shortages
- Manufacturing process breakdowns
- Labor strikes
- Port traffic jams
- Weather disasters
These delays are costly, too. When a large container ship got stuck in the Suez Canal, it was estimated that each day of blockage disrupted $9 billion worth of goods.
Unfortunately, the vast, complex nature of supply chains means more potential for bottlenecks. The key to building a resilient, agile network goes beyond understanding where these bottlenecks lie. You must also pinpoint their root causes, foresee the ripple effects through the network, and anticipate the outcomes of decisions. To do all this, you need technology that lets you analyze and interpret relationships between all the elements in your supply chain.
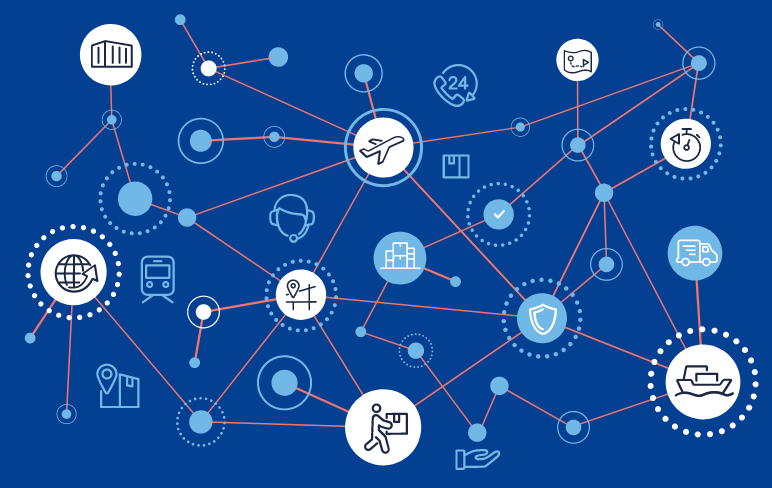
How to Improve Supply Chain Forecasting: Beyond Legacy Tools
Unless you have end-to-end visibility into your supply chain, you won’t be able to detect bottlenecks before they happen.
It’s exceptionally hard to map out interconnected, unstructured data from different sources when you rely on spreadsheets or relational databases. Faced with complex datasets, relational databases become clunky and lose fidelity, which prevents efficient, agile demand forecasting in supply chain.
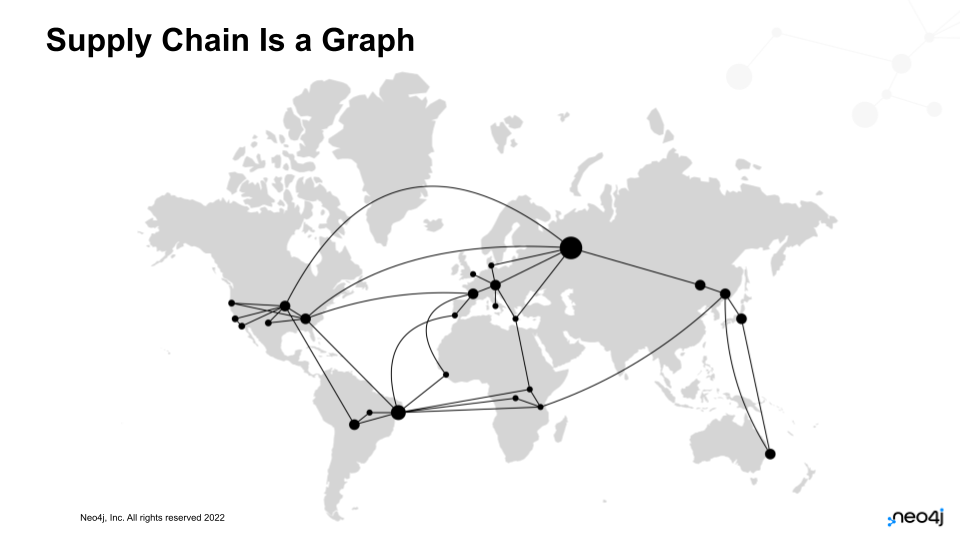
Supply chain leaders are transforming their data systems to enable stronger forecasting in supply chain management, with the goal of predicting, mitigating, and avoiding disruptions altogether. McKinsey reports that 90 percent of supply chain executives expect to overhaul their planning technology within the next few years. 80 percent are already embracing AI, machine learning, and data analytics to improve their processes and discover previously out-of-reach insights.
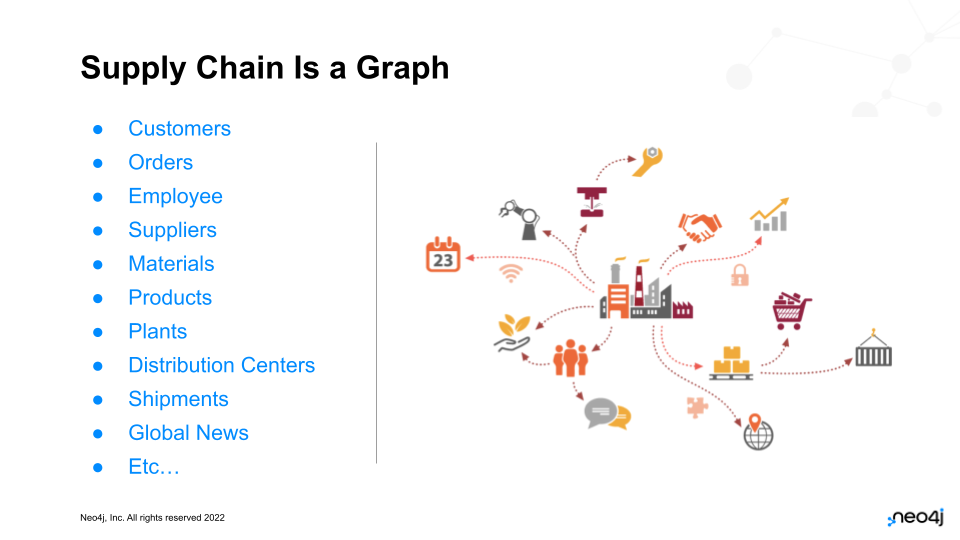
Graph databases are designed to support end-to-end visibility for the modern supply chain, allowing you to see your supply chain as it exists in the real world: a network of entities.
How to Visualize Your Supply Chain With a Graph Database
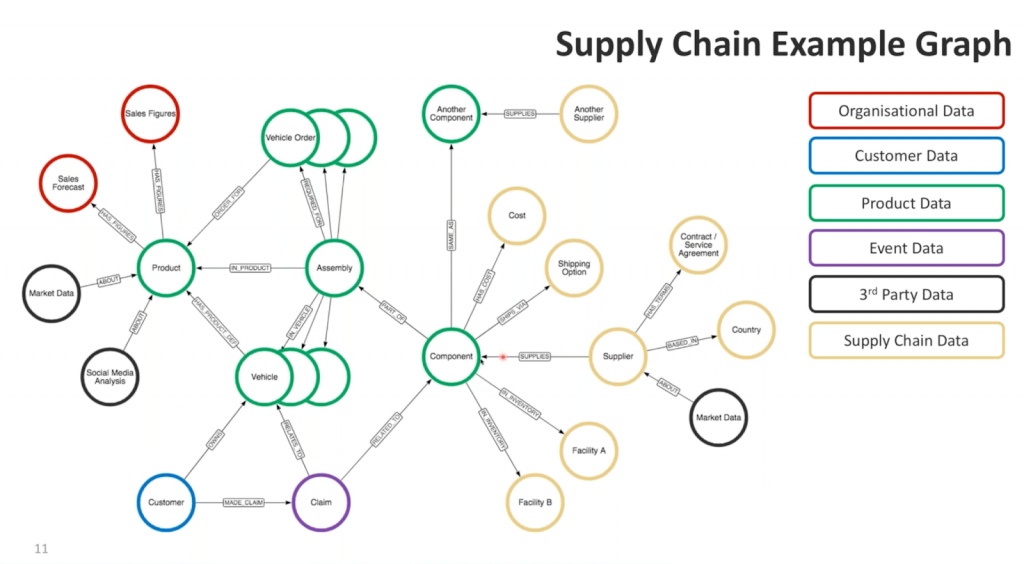
To enable accurate supply chain forecasting, your database should capture the relationships between entities (called “nodes” in a graph) such as suppliers, pathways, distribution centers, products, and so on.
A graph database enables you to map out these elements of your supply chain as interconnected data points with clear relationships. Since graph databases are schema-free, they easily adapt and expand to incorporate new data, whether that’s from another supplier or a new product category.
Besides providing an intuitive visualization of your supply chain, graph databases offer another much-needed benefit: speed. Unburdened by rows, columns, JOINs, and inflexible frameworks, graph databases can deliver 100 times faster query responses than relational databases. That’s because the relationships between entities in your supply chain become first-class citizens in a graph database. For supply chain forecasting, working with your data as a set of relationships allows you to make more accurate predictions.
4 Most Popular Graph Algorithms for Supply Chain Optimization
With your supply chain data stored in a graph database, it’s simple to apply algorithms to conduct supply chain predictive analytics and extract insights. When you need to reroute or create a shorter path to react to situations such as a parts shortfall, you can traverse the paths of your supply chain in real-time.
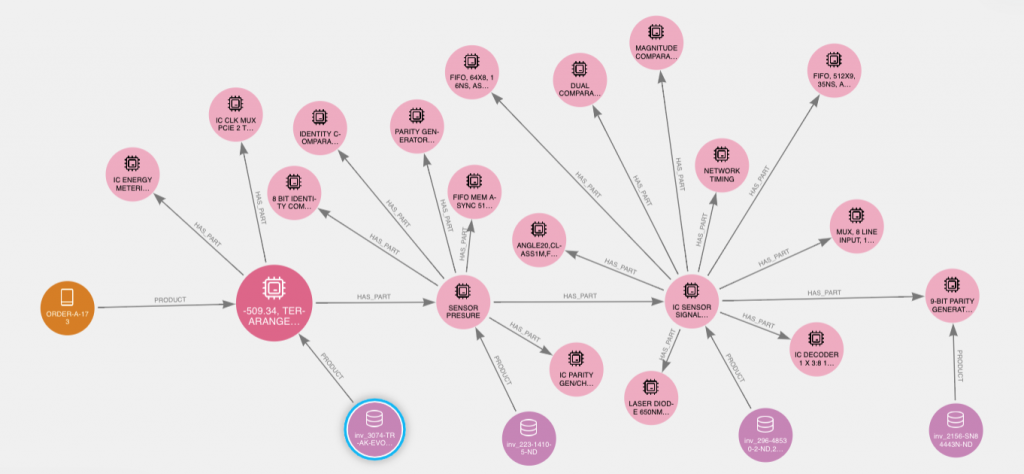
What are some key examples of predictive analytics in supply chain? There are four main algorithm categories for this use case. (Neo4j Graph Data Science contains 65+ predictive analytics and ML algorithms to help improve your models.)
1. Pathfinding and Search Algorithms
Pathfinding algorithms find and evaluate paths between nodes. Boston Scientific uses the Shortest Path algorithm to uncover links between faulty components. Other organizations use these algorithms to find optimal routes between raw materials and final products or the shortest paths between plants and distribution centers.
2. Centrality Algorithms
Centrality algorithms help you find the most important nodes in your supply chain, such as one element that connects to many others. When you use graph visualization with these algorithms, it’s easy to see potential bottlenecks like a heavy operational load on a central transportation hub – and how to bypass them.
For example, a supply chain manager could have used a centrality algorithm to forecast the massive Oakland and Los Angeles port bottlenecks that occurred in 2021. They then could have switched to on-shore suppliers to avoid costly delays.
3. Community Detection Algorithms
Community detection algorithms evaluate how node groups are clustered or partitioned along with their tendency to break apart or become stronger. For example, if a part or raw material is found to be defective or contaminated, community detection algorithms can trace every product that contains the faulty element.
4. Similarity Algorithms
Similarity algorithms let you calculate similarities between nodes based on properties or closeness in a data set. This type of algorithm is helpful when you need to find alternative suppliers for comparable parts.
Real-World Example: Anticipating the Demand and Costs for Parts
The U.S. Army has adopted graph technology to transform its parts procurement and logistics from small arms to aircraft. (To give you an idea of the scale, the Army sometimes orders millions of components at a time.)
The Army had an aging mainframe-based system that needed help managing data queries like forecasting the need for replacement parts and calculating the mean time to failure. With Neo4j, the Army modernized this core tracking system, employing a 3TB database with over 5.2 billion nodes and 14.1 billion relationships to rapidly store, explore, and visualize its wealth of logistical data.
Now, the Army anticipates the demand for spare parts and spreads it across multiple budget time periods. That means better ordering and budgeting, with a more predictable total cost of ownership – and not at the cost of equipment downtime or safety.
The Value of Graph
In any key business role – be it CIO, CTO, Director of Data Science, supply chain leader, or lead developer – it’s imperative to have empirical evidence when investing in a new technology.
Forrester Consulting conducted a Total Economic Impact™ assessment of Neo4j, an industry-standard framework that’s been used for the last 20 years. This method examines costs, benefits, flexibility, and risks to provide an informed projection of the product’s return on investment.
This commissioned study calculated the average value of using graph technology across customer deployments. It found that a composite organization could expect Neo4j to pay for itself more than 4x in the span of three years, delivering a 417 percent return on investment (ROI).