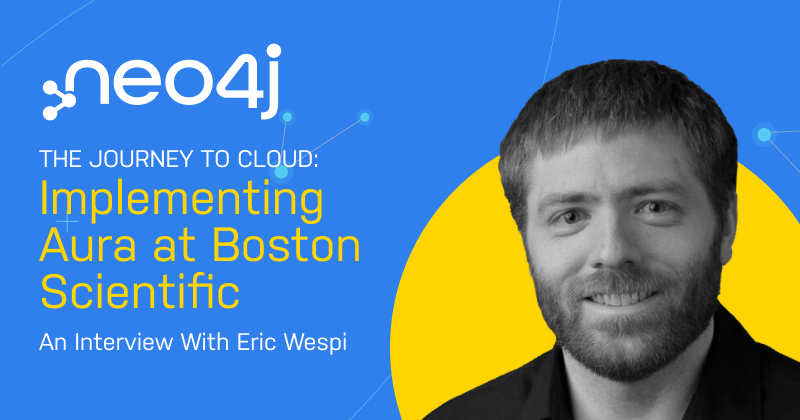
If you missed this year’s Neo4j and the Cloud digital Connections event, fear not! You can still peruse our video archive to get a sampling of what we were offering, and pretend you were there all along. We spoke with thought leaders and experts in the graph database space to learn more about their work and how they use Neo4j. We explored AuraDB (our own fully managed cloud solution), gained insights into the future of graphs in the cloud, heard from a few database architects and graphy executives, and more.
Here’s an interview we did with Eric Wespi from Boston Scientific. Eric manages a data science team within the manufacturing side of the company and offers here a fascinating look into a real-world use case of a Neo4j customer.
Enjoy, and don’t forget to stay tuned for more blogs from our 2021 Connections events.
Greta Workman: I have with me today Eric Wespi from Boston Scientific. Eric and his team have been Neo4j users for quite some time now but have recently joined us on AuraDB Enterprise. So we’re going to talk a little bit about their journey with Neo4j, how they’re using it at Boston Scientific, and a little bit about AuraDB Enterprise as well. So Eric, let’s just start by having you introduce yourself and Boston Scientific.
Eric Wespi: Thank you Greta. My name is Eric Wespi. I manage a data science team at Boston Scientific and we work within the manufacturing organization. Boston Scientific’s a large company making medical devices. We’re pretty highly vertically integrated and we’re within the manufacturing and operations organization.
Greta Workman: Cool, and can you describe a little bit about how you guys are using Neo4j?
Eric Wespi: Yeah i think, because we’re manufacturing, we’re focused on a couple key primary use cases. We’re looking at quality and investigations, understanding events that happen within our factories – how we can investigate the root causes and find solutions to those – and then more typical things like yield improvement and optimization of those processes. We’re exploring other things like understanding how our devices are used and how customers refer each other, things like that. But for now we’re pretty focused on the manufacturing and operation side.
Greta Workman: How does that work exactly? Can you talk a little bit about the high level data model and how Neo4j fits into that application?
Eric Wespi: Sure, so a single medical device represents the combination of dozens of components, often multiple factories, different countries involved, several different processing technologies. And so what our data model is is really a representation of those processes. We have nodes for batches or units, the different process steps they go through, certain measurements and other inputs to the overall process. And those nodes are all connected via the manufacturing transactions and the process steps that they go through. So we build that representation of the end-to-end internal supply chain, how we build apart from the beginning to the end, and what happens along the way, for some.
For example, you could look at our graph and you can almost infer what the bond is, where everything went into a part, for example.
Greta Workman: That’s great. How were you doing that before you brought Neo4j in?
Eric Wespi: It was a bit of a mess. In some cases it just wasn’t being done, so some of these quality investigations – the types of analysis that we’re doing now – just weren’t really happening because it was challenging. In other cases it was just a collection of SQL queries with a number of relational databases that have this information, a bunch of excel sheets, so there was general frustration and hand wringing. So it took a lot of time. It was really complex manual work by engineers – and usually it was engineers, it wasn’t data analysts – so people that aren’t familiar with the databases pulling data trying to put it together in a meaningful way. They didn’t really have the tools to put that together in the complex supply chain for analysis. I think what that leads to, and what it was leading to, is that an engineer would go spend, you know, days or weeks on these analyses, and then they’d come back and no one in the room would be certain of the results. So there was just a lack of standardization and a lack of confidence in what we were doing.
Greta Workman: So what made graphs the right solution and how is it helping your application there?
Eric Wespi: I think because we can represent that entire supply chain and we can have it loaded and ready we’re not doing a lot of the work of that analysis, which is to put the data together. So now putting the data into the database can be a simple script that can be validated and understood. There’s a lot of speed in doing that work, and there’s also additional analysis capabilities. So when you’re doing those things manually you’re making decisions about what data you’re getting and how you’re getting it. And there’s certain analysis that just doesn’t really work on a long complex path in Excel. So that’s the speed and the capabilities but I also think another one is just the standardization of the approach. We’re not wondering how someone did something because they used it the way that we’ve prescribed. I think those are really big benefits to how we go about like a quality investigation.
Greta Workman: And you guys are doing some analytic work on top of that too, right? Can you talk a little bit about the graph analytics part of it as well?
Eric Wespi: Yeah, so when we load all that data in we might have some kind of event – a quality type of event at the end of the line, say – and so what we’re trying to do is highlight and conduct the root cause analysis of what might cause that event. If it’s manufacturing related, we don’t know where to start, so we’re trying to direct teams and say which material, which batch, which process might have been most correlated with that quality event or number of events.
Some of them are really straightforward. I mean, we don’t have to go into super complex page rank algorithms or really complex graph algorithms – just the structure itself allows us to do chi-square analysis or basic scoring methods where we can use common statistical techniques because of the way the data is structured. We have the data in there, but it’s not just the value of the data in relational databases, the value is that the relationships can be analyzed. So we put the data in the graph, calculate some features, assign those to the nodes or the relationships, and then we extract those features again. So we do some analysis to create features in Cypher and then when we pull that out we can do more standard statistical analysis.
Greta Workman: Cool. Can you walk us through what the process was for bringing Neo4j into Boston Scientific? How did this process start?
Eric Wespi: It’s a good question. It took a bit of time. When we started we were small – we’re bigger now – but we were a really small team. We started with Neo4j desktop or community edition back in the day, I think. We learned a lot. We started with, “Let’s just learn Neo4j, let’s learn Cypher.” There are a number of articles and training materials and stuff on the website. It was kind of like looking at these things – what do we see that inspires us? Do we have that same problem that could be solved in that way?
So it was about finding a good problem that aligns with this. And then we were working within the Neo4j desktop to demonstrate some value. “This could have some legs” say, or “You know we can solve a problem in this way” and then it was about finding a sponsor that could pay for a more capable license to grow that data set. After that, there were like two or three of us that knew this and were excited about it and we had someone paying for it. But then it was kind of like, “Let’s grow the internal community.”
That can be tough in a company – you know we’re not a tech company that has a whole bunch of people using graphs, right? So it was about really demonstrating the value to people and educating them. So if there’s plenty of people interested in analytics, you can say “Hey, let’s talk about graphs and what we can do with graphs.” And then you could find more use cases and more excitement in that way.
Greta Workman: For the project that you found, did you have any kind of metrics that you had to meet going into that, or any sort of like success goals that you were working towards? How did Neo4j help you meet those goals?
Eric Wespi: For us, the initial use case was really about quality investigations. It’s more about discovering things we wouldn’t otherwise be able to find and can we get to a root cause faster. So what we’ve done is some historical analysis where we already know what the root cause was and then we apply these algorithms and say “Well, would we have found the root cause using this graph?”
And so we can demonstrate the value and say, “Look, you’d find a response in a few minutes or an hour maybe using this analysis method. Whereas it took you months to find that root cause with the standard methods. And that’s a really compelling argument when you’re talking to Vice Presidents or whoever about what kind of technologies you can apply in those situations. So it’s about how long the analysis takes, but just looking at time savings isn’t really getting to the full story. It’s about finding things you wouldn’t otherwise be able to find.
Greta Workman: Yeah. And what has feedback been like from your internal users on this application? Have you gotten any feedback?
Eric Wespi: It’s been great. We have a lot of, I’d say, repeat customers, people saying, “You know, I’m on this other project now, I want to use this technology.” Calling us up and setting up meetings and things. Also what we see that’s really cool is we have some customers that are saying, “That’s really cool that you’re able to find that, I want to be able to do that too.” So getting them on the platform, teaching them how to use some basic Cypher queries, for example, teaching them about how this model is designed and getting them on the path to playing with it themselves. It’s kind of growing internal customers but also practitioners, which is really exciting.
Greta Workman: Yeah, and actually I want to double click on that as well, because I think that’s kind of a common reality for us at Neo4j. We have a couple of great champion customers that want to grow and spread the use of graphs within their company. Do you have any advice for people that are kind of similar to yourselves, as kind of the Neo4j gurus of their companies? How do you get the information out there in the world?
Eric Wespi: I mean, for me if you just talk about the technology it’s really hard to get that engagement. For us, it’s been about, “Hey we found this cool thing, we found a root cause really fast with some new technology” and they go, “Wow, I’m interested in that.” And then you can get into what a graph database is. I mean, I think just the display in the Neo4j browser gets people excited; they love seeing the bubbles and everything. So, depending on the audience, that can be another good method.
But I think it’s really about showing that the bar isn’t that high. When you can talk really technically about graphs and graph algorithms it can start to sound really intimidating. But I think if you start to show people some little Cypher things and play around with the data sets and stuff within Neo4j, you can start to show people that this isn’t a difficult thing. You can demonstrate how easy it is rather than how difficult it is, and I think that’s another good way to get people building a practitioner base.
Greta Workman: I love that. Alright, so let’s talk about AuraDB a little bit. So Boston Scientific has recently joined AuraDB Enterprise. Can you talk about why you guys felt like AuraDB was the right way to deploy Neo?
Eric Wespi: We’re really excited about it. As I said, I manage a data science team – we’re not an IT team, we’re not within IT. We aren’t database administrators as our initial efforts with Neo4j would demonstrate. So you know, we aren’t trying to keep the database running, make sure it’s configured properly, scaling properly, growing different data sets, things like that. We don’t want to focus on that. We don’t want to spend a lot of time on that. We’d rather spend our time on the data model analysis and on the movement of data in and out. So AuraDB really, because it’s a managed service it helps us focus on those things and focus on what we bring to the table and not all this other administrative stuff. And I’d say IT is really supportive of that, too. They don’t want to have a new database dumped on them to maintain, right? So yeah, it’s been really good.
Greta Workman: And how has the process been? Do you have any advice for people starting out on their AuraDB journey?
Eric Wespi: It’s been awesome. You know, it’s amazing. I got people reaching out. I have regular checkpoints. I submit a ticket and I’m like, immediately talking to developers and they’re pushing fixes and stuff. It’s amazing. It’s been really smooth for us. So yeah, I think just reaching out and getting started is great. I think the fact that you know at the different price points it scales really well, you know, like a pay-as-you-go service. So I think there are a lot of compelling reasons to get going.
Greta Workman: That’s awesome. So what’s next for the project at Boston Scientific?
Eric Wespi: You know, we started a little bit narrow within manufacturing in terms of how many databases we had. So for us, it’s about expanding and bringing new data sources in. When you start to whiteboard these things or play around with what that data model is it’s really easy for you to start brainstorming. Like, “What if we could also connect to this other thing” or “Let’s build an enterprise knowledge graph,” right?
So for us it’s about bringing in other data sources and seeing how that can help us solve the current problems better, but also what kind of new problems can we solve? So I think that’s where we’re at – like bringing in new data sources. And then also, kind of beyond manufacturing, how can we connect the supply chain and manufacturing to things that happen post-market? Or like, how our devices are used or designed. So it kind of goes in a lot of different directions and it’s about engaging the practitioners and making sure that everyone’s empowered to start moving along those lines.
Greta Workman: I always kind of joke that once you bring in this kind of snowball of innovation, you kind of start being able to say yes to new projects and new ideas. And then it’s kind of like, all right what else can we do next?
Eric Wespi: Yeah, it’s amazing how it’s an engine for creativity and people just start to brainstorm all kinds of new use cases. So we’ve got all kinds of things going on.
Greta Workman: That’s great to hear. Well, thank you so much for joining us today. Everyone, that’s Eric Westpi from Boston Scientific.
Check Out Connections